Metal laser cutting machine are advanced tools used extensively in the manufacturing industry to achieve high precision in cutting various types of metals. Utilizing focused laser beams to sever materials, these machines have become essential for businesses that require accuracy and efficiency in their production processes. The core technology behind this method involves generating a powerful laser beam that is directed onto the metal surface, heating it to the point of fusion and effectively cutting through the material.
Several types of lasers are employed in metal laser cutting machines, the most common being CO2 and fiber lasers. CO2 lasers utilize a mixture of gases to produce the laser beam, which is particularly effective for cutting thick materials and provides a smooth edge finish. On the other hand, fiber lasers use a solid-state medium and are known for their energy efficiency and speed, making them ideal for a wide range of metal types, including stainless steel, aluminum, and brass.
Over the years, laser cutting technology has evolved significantly, moving from ancient mechanical cutting methods to modern automated systems. The advent of computer numerical control (CNC) has further enhanced the capabilities of metal laser cutting machines, enabling them to execute complex cuts with minimal human intervention. This evolution underscores the increasing significance of laser cutting in modern manufacturing, where precision, speed, and flexibility are paramount.
As industries continue to adopt metal laser cutting machines, their significance in streamlining manufacturing processes cannot be overstated. The integration of advanced technologies has not only improved efficiency but also reduced material waste, making laser cutting a sustainable choice for metal fabrication. Thus, understanding the mechanics of metal laser cutting machines and their components is crucial for industries seeking to leverage these technologies for competitive advantage.
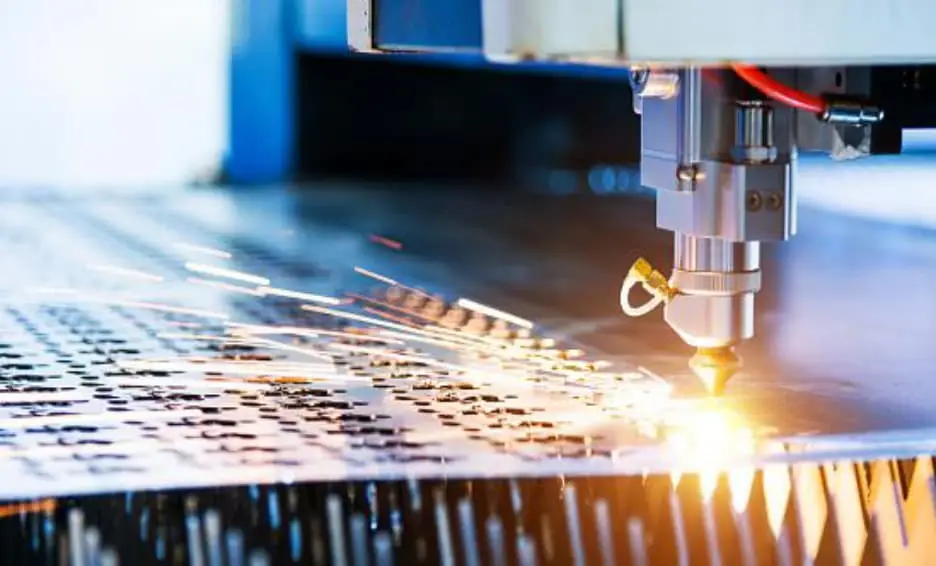
Applications of Metal Laser Cutting Machines
Metal laser cutting machines have revolutionized fabrication processes across multiple industries, notably in automotive, aerospace, electronics, and construction. The precision and efficiency provided by these advanced machines enable manufacturers to meet the increasing demands for complex designs and rapid production cycles.
In the automotive sector, metal laser cutting machines are utilized to create intricate parts, including chassis components and brackets, with exceptional accuracy. Their capability to handle various metals, such as stainless steel and aluminum, ensures that automotive manufacturers can produce lightweight yet durable components that contribute to vehicle efficiency. For instance, companies have adopted laser cutting technology to manufacture high-strength steel parts, which improves overall vehicle performance while maintaining safety standards.
Aerospace is another industry that greatly benefits from metal laser cutting technology. The strict tolerances required for aircraft components can only be achieved through advanced cutting techniques. Metal laser cutting machines create complex geometries in materials resistant to high temperatures and stresses, such as titanium and superalloys. This capability allows aerospace engineers to design innovative structures that enhance fuel efficiency and performance. For example, the production of turbine blades and other critical components relies heavily on the accuracy of laser cutting processes.
In the electronics industry, laser cutting is essential in producing circuit boards and housings with precision cuts that minimize material waste. Companies can implement sophisticated designs and intricate patterns to meet the miniaturization demands of modern electronics, leading to lighter and more compact devices.
The construction sector employs metal laser cutting machines for fabricating structural components. The ability to customize and produce complex shapes on-site enhances construction efficiency, reducing labor costs and project timelines. Various examples illustrate how this technology supports modular construction and prefabricated components, ultimately streamlining the building process.
In summary, the applications of metal laser cutting machines are vast and varied, providing a critical advantage in industries striving for greater precision, efficiency, and the ability to execute complex designs.
Advantages of Using Metal Laser Cutting Machines
The utilization of metal laser cutting machines offers a multitude of advantages, transforming the landscape of metal fabrication. One of the most significant benefits is the superior accuracy these machines provide. Laser cutting technology allows for intricate designs to be executed with precision, thereby reducing the margin for error and elevating the quality of finished products. This high degree of accuracy is particularly advantageous in industries where specifications must be tightly adhered to, such as aerospace and automotive manufacturing.
Additionally, metal laser cutting machines contribute to reduced material wastage. Traditional cutting methods often result in a considerable amount of scrap material, which can inflate costs and negatively impact environmental sustainability. In contrast, laser cutting permits more efficient use of materials, as it typically requires less cutting length and more closely follows the desired contour of the parts being produced. This efficiency results in significant savings for manufacturers and a reduced carbon footprint.
Another noteworthy advantage is the speed at which laser cutting machines can operate. Due to their advanced technology, these machines can process materials quickly, leading to faster turnaround times for projects. This enhanced productivity can be particularly beneficial in high-demand environments where time is a critical factor. Moreover, lower operational costs are another compelling reason to adopt laser cutting technology. The reduced need for manual labor, coupled with lower energy consumption, means that businesses can operate more economically.
Workplace safety is also improved with the use of metal laser cutting machines. Laser technology minimizes the physical interaction workers have with sharp tools and dangerous machinery, thus fostering a safer work environment. Furthermore, these machines can handle a variety of metal thicknesses, making them versatile options for a wide array of project specifications, from delicate to heavy-duty applications.
In conclusion, the advantages of employing metal laser cutting machines are numerous, impacting accuracy, material efficiency, speed, cost-effectiveness, safety, and adaptability in metal fabrication.
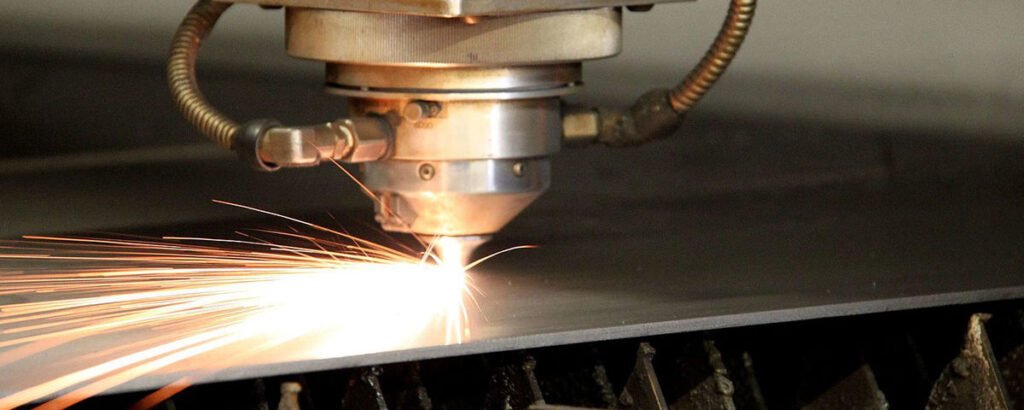
Future Trends and Innovations in Metal Laser Cutting Technology
As industries continue to evolve, the landscape of metal laser cutting technology is also experiencing significant advancements. One of the foremost trends is the increasing automation within the fabrication processes. Automation enhances productivity and efficiency, allowing metal laser cutting machines to operate with minimal human intervention. Robotics and automated workflows are expected to become standard, streamlining the cutting process and reducing lead times, which is crucial for meeting the demands of modern manufacturing.
Moreover, the integration of artificial intelligence (AI) is set to revolutionize how metal laser cutting machines function. By employing AI algorithms, these machines can optimize cutting paths, assess material requirements, and predict maintenance needs. This smart integration not only increases the precision of cuts but also offers data-driven insights that enhance overall operational efficiency. AI’s role will likely expand, making laser cutting processes more adaptable to varying production demands and complexities.
In addition to these technological advancements, the laser sources themselves are undergoing innovation. Developments in fiber laser technology and solid-state laser sources are resulting in machines that are not only faster but also more energy-efficient. Greater energy efficiency translates to lower operational costs and a reduced carbon footprint, aligning with the growing industry focus on eco-friendly manufacturing processes. The demand for sustainable practices is prompting manufacturers to invest in technologies that minimize waste and optimize resource usage during the cutting process.
Looking ahead, we can expect a confluence of these trends to shape the future of metal cutting technologies. The emphasis on automation, AI integration, and eco-conscious manufacturing will guide the next generation of metal laser cutting machines. These innovations will enable industries to respond more effectively to market demands, enhance productivity, and maintain a competitive edge in an ever-evolving manufacturing landscape.